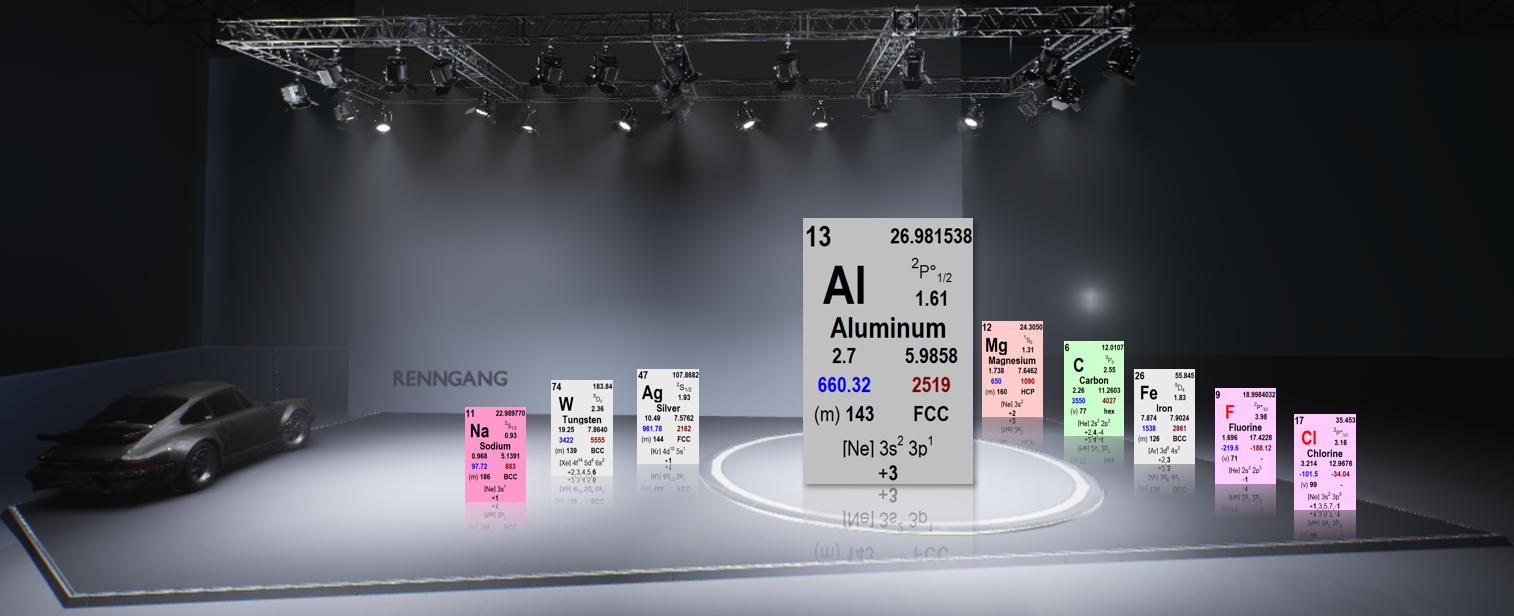
Aluminum has a lower specific weight than steel, and we don't have the same corrosion problems as with other metals.
Aluminum is the most common metal found in the Earth's crust. Around 8% of the Earth's crust consists of aluminum, but it does not exist in metallic form like gold does in gold veins. The raw material from which we extract aluminum is called bauxite.
In a historical context, aluminum is a relatively new material. After World War II, aluminum production took off. The metal aluminum wasn’t discovered until well into the 19th century, and it took a long time before an efficient industrial production method was found.
1825 was the year aluminum production was discovered. At that time, it was a very expensive metal—even more expensive than gold. A well-known anecdote is that Napoleon used aluminum plates for his most honored guests, while regular guests had to settle for gold.
Toward the end of the 1800s, the Bayer and Hall-Héroult processes were developed for aluminum production. From the early 1900s onward, it became possible to use aluminum in construction.
Today, aluminum is widely used in car parts.
The advantages of aluminum are that it has a low weight-to-strength ratio, it is recyclable, and it is corrosion-resistant. The reason aluminum doesn’t rust is that when the surface is exposed to air, it reacts with the oxygen to form a thin, strong layer of aluminum oxide, which gives it a slightly dull appearance. This layer is dense and strong, protecting the inner aluminum from external influences. You can see this on the gearbox and engine of a Porsche 911 if they are made from aluminum.
Aluminum also has good durability, it's formable due to high ductility, and it has good electrical conductivity.
We have two main methods of producing aluminum:
From raw bauxite
From recycled materials (secondary production)
We can use electrolysis for production, though it requires a lot of energy. But before we get to electrolysis, we have to go through several steps, such as extracting the bauxite. It needs to be crushed, and unwanted minerals must be removed. The goal is to end up with a substance called alumina, which is an aluminum oxide compound. After this, we proceed with electrolysis, which produces pure metallic aluminum.
In principle, carbon electrodes are used to dissolve the aluminum oxides in an acid bath.
It takes about 12–14 kWh to produce 1 kg of aluminum.
There is a 1:4 ratio of how much bauxite is needed to produce aluminum. So from 4 kg of bauxite, we get 1 kg of aluminum.
Aluminum also has a relatively low melting point of 660°C, compared to pure iron, which melts at 1500°C. So remelting aluminum only requires about 5% of the original energy input. Many researchers are working on new recycling systems for aluminum.
One of the challenges is that a lot of aluminum is alloyed, and sorting it out is difficult.
The density of aluminum is about 2.7 kg per cubic decimeter. That means if we have a solid block measuring 10x10x10 cm, it weighs 2.7 kg if made of pure aluminum.
Compared to iron, which would weigh 7.87 kg, aluminum is about 1/3 the density of iron.
The price per kilogram of aluminum, although it varies, is about three times the price of iron. However, on a volume basis, aluminum is cheaper since it takes up more space.
We've talked a bit about the advantages of aluminum, here are some disadvantages:
It has a low modulus of elasticity compared to steel (i.e., less stiffness relative to strength).
It has limited applications at high temperatures due to its low melting point (660°C).
It has a relatively high material cost compared to steel.
It has low fatigue strength compared to steel.
It is softer in deformation compared to load-bearing capacity.
The reason aluminum is so easy to shape is because it has a face-centered cubic (FCC) crystal structure, with many closely packed atomic planes, allowing for slip at relatively low applied stresses.
To make aluminum stronger, it needs to be alloyed.
The most common alloying elements are magnesium and silicon, which make the alloys stronger and heat-treatable. Magnesium also improves weldability. Copper is also used, providing heat-treatable alloys that become stronger with heat treatment.
In pure aluminum-magnesium alloys, usually no more than 5–6% magnesium is used, to avoid getting too much of the beta phase.
In addition to these, other alloys are used to achieve special properties, like improved castability. These typically involve less than 0.1% of additional elements.
Aluminum can be divided into wrought alloys (for plastic deformation) or casting alloys.
We can strengthen aluminum alloys through:
Cold working
Precipitation hardening (by alloying)
Particle strengthening